Step 1) Starting with
disassembly, place the model on your workbench, desk or table to access
the top of the loco and the end of the tender. First remove the screw at the rear end of the tender
and place where it can be found for reassembly in the original hole it
came from. Pick up on the rear of the tender shell about a half inch
while holding the rear truck then
slide the shell forward about a quarter inch. the metal tab on the front
of the frame should disengage with the shell. place the shell out of the
workspace to protect it. |

|
Step 2) Remove the screw at
the top of the cab and place it where it can be located for the return
to the same hole |

|
Step 3) Remove the smokestack
insert. Use a regular screwdriver capable of fitting into the slots cut
in the top of the smokestack and turn counterclockwise like removing a normal
screw. The Franklin unit originally had a brass insert although it could
have been replaced with a plastic one at some point. Same rules apply. |
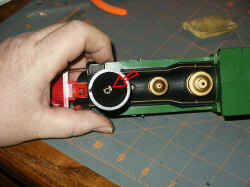 |
Step 4) Remove the side-rods
from the drivers using an appropriate method. Pliers can work for
removing the fasteners but the
odds are great of scratching the screws and the side rod. A socket type
wrench is best for this one. Remove the drive rod from the wheel post
and slide the driver with the steam chest rod out of the frame and place
it somewhere out of your workspace. Repeat for the other side. Remember
which rod came from left and right. They may be bent individually for
clearances or you may have to straighten them for necessary clearance. |
|
Step 5) Remove the two screws under
the front trucks that hold the chassis in the shell. Place them in a
location to remember where they came from |
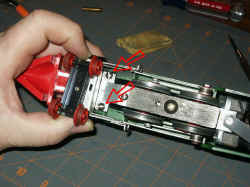 |
Step 6) Using the contact cleaner
OUTSIDE or in a very well ventilated area, clean the areas of the trucks
where the axles enter the side-frames and where the pickup strips
contact the axles. It appears to be ok to clean the wheels as well. I
have not noticed any degradation of material using the fast drying
solution. Clean both trucks in the same manner. |
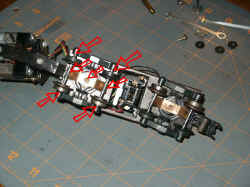 |
Step 7) Next clean the moving portion
of the e-unit. Try to stay away from the coil when spraying the oils
off. Generally this is clean from debris, but sometimes people put oil
on the mechanism to aid in its function, but the results are short lived
and the unit gets sticky refusing to change direction without
assistance. Always keep this unit clan and dry. It needs no oil. |
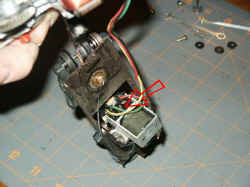 |
Step 8) Spray clean the front journal
and worm drive of the armature to release old oils, fines, and tar
buildup from previous years of use. |
 |
Step 9) Finally, clean the rear
journal and commentator. As with the e-unit, try to stay away from the
windings. The wires are coated with a shellac and may be susceptible to
different kinds of contact cleaner. Better safe than sorry. |
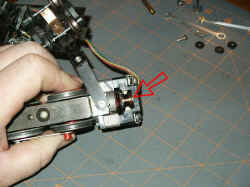 |
Step 10) In the case of this
locomotive, the major reason for the hesitation and requirement for
tapping to get it going was due to the spring pickups loose on the
rivets. Hold the truck with one hand and swivel the pick-up from side to
side to check tightness of rivet. If it moves easily, then the current
can not make it through to the wire soldered to the other end. Using a
flat punch or a rivet tool, peen the flange over a little tighter. Remember
you are working on a delicate electrical unit, not constructing a
skyscraper, so tap gently and check for snug movement many times. |
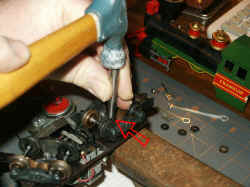 |
Step 11) Next lets make sure the
contact is made between the pick up strip and the axle. When the unit is
upside down touch the wheel and push down gently. the strip should be
showing pressure on the axle by raising the axle in the side-frames. To
regain the tension, hold the end of the strip with one finger while
pushing lightly on the spring about 3/8 of an inch from where it bend
up. Push a little and check a lot. It is right when the axle picks
itself up from the bottom of the holes in the side-frame. Repeat for
remaining three strip ends and axles. |
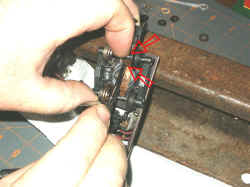 |
Step 12) Lets talk Oil. Any oil on the
motor that is extra will end up inside the engine shell or on the track
and wheels of all your moving stock and engines and that is guaranteed. Oil the front armature shaft bushing. Use oil
that is approved for plastics. It is a synthetic blend that will not attack the
shell. Place a couple drops on the shaft between the thrust washers and
the chassis. The oil- lite bushing will absorb some oil due to its
porosity and this will maintain lubrication for many hours. No more than
3-4 drops is needed for performance. |
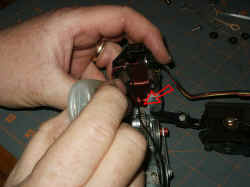 |
Step 13) Lubricate the brush end of the
armature. 2 drops is generally sufficient. Extra oil on this end will
cause brushes and commentator to get gummy and carbon up causing issues
so keep it lean. |
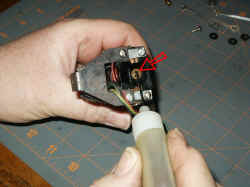 |
Step 14) Lubricate the gear pin and
bolt for the smoke unit arm. A couple of drops is all that is necessary.
Do not oil the teeth of the gear or the lithium grease will not stick.
It generally is not necessary to oil the other end of the drive rod but
it does not hurt anything. extra oil in the chuff chamber where the
piston runs will lubricate the sides and reduce the volume of the
chuffing sound. |
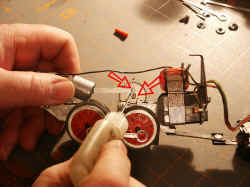 |
Step 15) A lubricant that I found that
works very well for contact on the pick ups is Anti-Seize or sometimes
called Never-Seize. It is used in the automotive industry to for
applications to threads and pins that you wish to remove at a later
time. Anti-Seize is made of Copper Powder, Aluminum Powder, Zinc Oxide,
and Graphite. These components are all conductors of electricity and
work very well on the pick ups to ensure contact and prevent oils and
debris from becoming an insulator. Using a tooth pick place a little on
the axle near the copper strip and rotate the wheel set. |
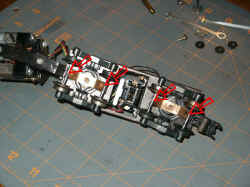 |
Step 16) White lithium grease or Gear
lube at a hobby store is the lubricant of choice for the worm and drive
gears. the worm distribute the lubricant during operation between the
gears so you only need to put some on the top of the chuff drive gear.
spread it out with a tooth pick after adding. |
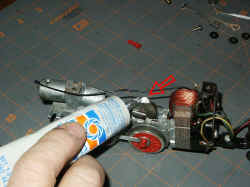 |
Step 17) Reassembly is next. The
Franklin may or may not have rubber washers that insulate the sound
between the locomotive shell and the chassis. If yours does use a small
drop of general purpose adhesive on the back side of the washer and
place it over the hole that it covers. The deformation of the washer
should reflect which hole it came from and the adhesive will keep it in
place while you assemble the chassis to the shell. Next drop the chassis
into the shell lined up to the holes. |
|
Step 18) Reinstall the screws that hold
the chassis front in place. Do this with extreme gentleness. This is
done by feel and generally is the primary cause in broken screw posts on
loco shells. When the plastic gets old it gets brittle. The screw
threads MUST find the original threads in the plastic boss made by it
from original assembly. Drop the screw into the hole and with a small
screwdriver turn gently clockwise. If resistance occurs, do not force
it. Turn it counterclockwise until you can feel it drop down a little
and try again. Make sure screw is straight. Make only snug. |
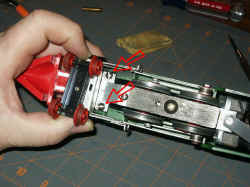 |
Step 19) Install the screw in the cab
following the same procedure as the chassis. forcing will cross thread
the steel bracket and the screw will never tighten up again. |
 |
Step 20) Install the brass insert in
the smokestack using a screwdriver that captures both sides of the slot.
too small will break the slot. Make sure it is straight and it follows
the same procedure as the threads above. The insert screws into a fiber
plate which can be cross threaded easily as well. General rule of thumb
is to feel for resistance ant back it up until it drops a little, then
start again. This procedure uses the same feel as picking robin eggs
from a nest. Use care and two fingers. |
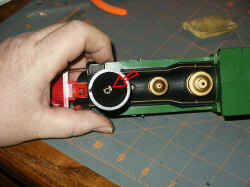 |
Step 21) Install the rear
tender shell by moving the wiring harness off to the right side of the
bar that connects the tender to the engine and mating the tab on the
front of the tender frame with the slot in the tender shell. The tender
frame will slide back into the recess of the lower tender shell and the
fastener hole in the frame should line up with the hole in the rear of
the tender shell. Use the same care as shown above. There is no
"snap in place" situation here and if it is not freely lining
up check the wire harness and alignment for binding or the front slot
will break in the tender shell under force. Capture the original threads
as defined above. |
 |
Step 22) Now that it is all together
lets check the trucks to see
if they are twisted. Objective is to have all four wheels touching the
track on both trucks at the same time all of the time. Place a couple
sections of straight track together on your bench and place the
locomotive on them. View the spacing at the point where the wheels meet
the track as you slowly tilt the tender away from you. Each pair should
leave the track at the same time and contact the track at the same time
when unit is returned. If they do not touch at the same time the truck
is twisted and needs to be straightened. Remove the train, use slight
finger pressure by twisting the trucks opposite direction holding both
frames of the truck. Do not put twisting pressure on the rivits or you
will need to redo Step 10. Twist a little, check a lot. They bend
easily. If wheel pair is not touching at all or very little, the side
frame may be bent up or other truck frame may be bend down. Repeat on
the other truck and the other side. When all four pair touch and move
within the frame slots the same amount you are done. Give it a try. If
still issues the problem may be in the motor or e-unit with spring
pressures or worn or burned brushes. |
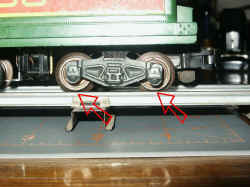 |